Moldflow Simulation in Injection Molding Process Optimization
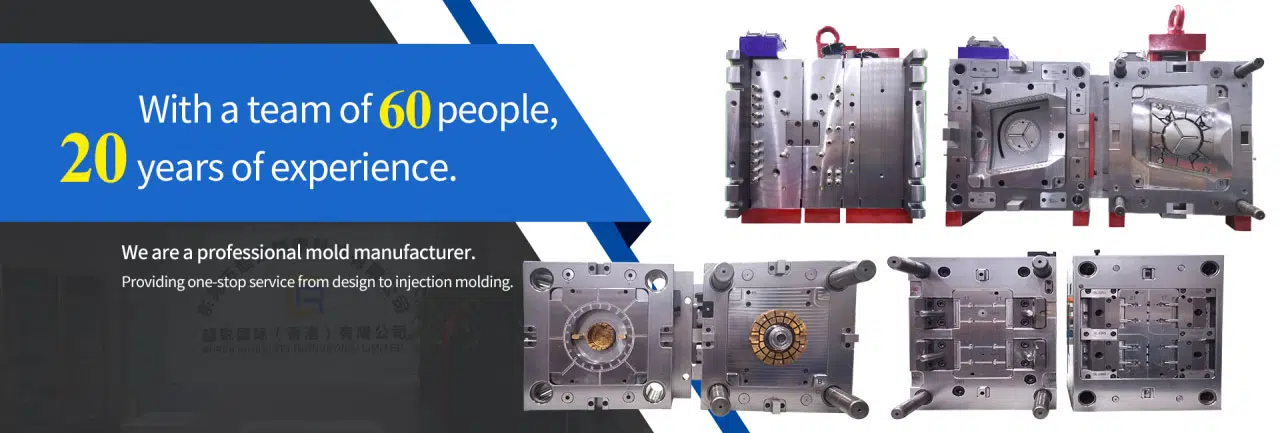
。
# Moldflow Simulation in Injection Molding Process Optimization
## Introduction to Moldflow Simulation
Moldflow simulation is a powerful tool used in the injection molding industry to optimize the manufacturing process. By leveraging advanced computational techniques, engineers can predict how molten plastic will flow into a mold cavity, identify potential defects, and make necessary adjustments before physical production begins.
## The Importance of Injection Molding Process Optimization
Injection molding is one of the most widely used manufacturing processes for producing plastic parts. However, without proper optimization, manufacturers may face various challenges:
– High scrap rates due to defects
– Increased production costs
– Longer cycle times
– Poor part quality
Keyword: Moldflow Simulation
Moldflow simulation helps address these issues by providing valuable insights into the molding process before any material is wasted.
## Key Benefits of Using Moldflow Simulation
### 1. Predicting and Preventing Defects
Moldflow simulation can identify potential problems such as:
– Warpage and shrinkage
– Sink marks
– Short shots
– Weld lines
– Air traps
By detecting these issues early, engineers can modify mold designs or process parameters to prevent defects in the final product.
### 2. Optimizing Material Usage
The simulation helps determine the optimal:
– Gate locations
– Runner sizes
– Cooling channel layouts
– Packing pressure profiles
This optimization leads to reduced material waste and improved part quality.
### 3. Reducing Development Time and Costs
Traditional trial-and-error methods in injection molding can be time-consuming and expensive. Moldflow simulation significantly reduces:
– The number of physical prototypes needed
– Mold modification costs
– Time-to-market for new products
## How Moldflow Simulation Works
The simulation process typically involves these steps:
– Importing the CAD model of the part and mold
– Defining material properties
– Setting up process parameters
– Running the analysis
– Interpreting results and making adjustments
Advanced simulations can analyze multiple aspects including:
– Fill phase analysis
– Packing and cooling analysis
– Warpage prediction
– Fiber orientation (for fiber-reinforced plastics)
## Real-World Applications
Moldflow simulation is used across various industries:
– Automotive components
– Medical devices
– Consumer electronics
– Packaging
– Aerospace parts
For example, in automotive applications, simulation helps produce lightweight yet durable parts with complex geometries while maintaining tight tolerances.
## Conclusion
Moldflow simulation has become an indispensable tool in modern injection molding operations. By enabling virtual testing and optimization of the molding process, it helps manufacturers achieve higher quality products, reduce costs, and shorten development cycles. As simulation technology continues to advance, its role in injection molding process optimization will only grow more significant.